NEI’s New Coating Technology Provides Self-Healing Protection for Traditional Coating Systems
March 24, 2015
Somerset, New Jersey (USA) – NEI Corporation announced today that it has introduced NANOMYTE® MEND-RT, a self-healing, polymer nanocomposite coating for use as an intermediate layer in coating systems on metal substrates. When the coating system is physically damaged, the self-healing intermediate layer repairs the damage autonomously at near ambient conditions, closing and sealing the gap and protecting the metal from exposure to the elements. This new feature of physical gap closing provides an alternative to chemical self-healing observed in chromate coatings. The universal nature of this new technology makes it applicable in any chromate-free coating system where self-healing is desired. This unique feature can lead to preserving the aesthetics of a coated surface or providing active corrosion protection on metal surfaces, without changing the formulation of the conventional coating. The intermediate layer can be easily applied by dip, spray, brush or drawdown methods.
The MEND-RT layer is introduced in a traditional coating system without deteriorating the original properties of the coating stack. The technology is applicable to coatings on both ferrous and non-ferrous metals and alloys, such as magnesium, aluminum, copper, zinc and alloys thereof, and steel. The efficacy of the NANOMYTE® MEND-RT coating was confirmed on aluminum alloys, which are used extensively in the aerospace industry. Two sets of coating systems were applied and compared for corrosion resistance. The first coating stack consisted of a chromate-free corrosion resistant pretreatment, a chromate-free epoxy primer, and a standard polyurethane topcoat. The second stack was identical to the first one, with the additional MEND-RT layer inserted between the primer and topcoat. Corrosion resistance was evaluated using the Salt Spray Test (SST) ASTM B-117 method. Artificial defects were made on the coated panels before exposing them to salt spray. The first set of panels, i.e. without the self-healing inter-layer, exhibited early signs of corrosion with white corrosion buildup in the scribed region. The samples with MEND-RT showed enhanced protection with no signs of corrosion after 1,250 hours of exposure.
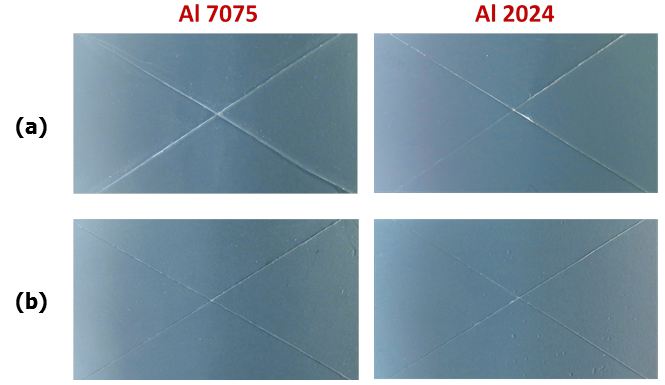
Photographs showing trends in corrosion resistance for Al 2024 and 7075 4” x 6” panels after 1,250 hours in salt spray test – (a) Commercial non-chromate coating system; (b) Commercial non-chromate coating system with NANOMYTE® MEND-RT.
NANOMYTE® MEND-RT is available as a two-part product. Given that different applications utilize a variety of coating systems, NEI can undertake an in-house study to evaluate the efficacy of MEND-RT in the specific coating system used by the customer. If needed, the MEND-RT formulation can be customized to suit the requirements of the application. Alternatively, customers also have the option of purchasing MEND-RT and applying the coating at their facilities or through their vendors.
Additional Technical Information:
- Technical Brief – A New Approach To Using Self-healing Coatings
- Technical Data Sheet (TDS) – NANOMYTE® MEND-RT
- Material Safety Data Sheet (MSDS) – MEND-RT (Part A)
- Material Safety Data Sheet (MSDS) – MEND-RT (Part B)
About NEI Corporation:
NEI Corporation is an application-driven company that utilizes nanotechnology to develop and produce advanced materials. The company’s core competencies are in synthesizing nanoscale materials and prototyping products that incorporate the advanced materials. NEI offers an array of Advanced Protective Coatings for metal and polymer surfaces. The coatings have tailored functionalities such as anti-corrosion, self-healing, scratch resistant, impact resistant, ice-phobic, and self-cleaning.
For more information, contact:
Ms. Krista Martin
(732) 868‐3141
sales@neicorporation.com
###